
A formulation of methylammounium iodide (MAI), PbCl2 and PbI2 at a molar ratio of 1:1:4 (PbCl2:PbI2:MAI) in a DMF solvent. On processing, I201 ink can be used to create a CH3NH3PbI3-xClx perovskite film. The process recipe for I201 is optimised for glove box processing under a nitrogen atmosphere.
I201 perovskite ink is divided into 10 lots of 0.5 ml. We have found this quantity to be sufficient for 10 individual experiments (approximately 160 device substrates).
Datasheet
We have specially formulated I201 Perovskite Ink in our laboratories to make it suitable for deposition by spin-coating. It is based on similar ink formulations used in references [1]. This ink is designed to be used with a bottom ITO/PEDOT:PSS anode and a top PC70BM/Ca/Al cathode, with PV devices fabricated with an average / peak power conversion efficiency (PCE) of (11.2% ± 0.4)% / 11.8%. This performance level is in accord with other literature reports using similar ink formulations where PCEs of approximately 11.5% have been demonstrated [1]. A full process recipe comes with the ink, which is ready to use after heating for a short time.

References (please note that Ossila has no formal connection to any of the authors or institutions in these references):
- Reproducible One-Step Fabrication of Compact MAPbI3-xClx Thin Films Derived from Mixed-Lead-Halide Precursors, D. Wang et al., Chem. Mater., 26, 7145-7150 (2014) DOI: 10.1021/cm5037869
Specifications
Perovskite precursor ink formulation: Ink I201 is based on a mixture of methylammonium iodide (MAI), lead chloride (PbCl2) and lead iodide (PbI2) at a molar ratio (PbCl2:PbI2:MAI) of 1:1:4 dissolved in anhydrous DMF (dimethylformamide).
Compound | Purity | Molar Ratio |
---|---|---|
MAI | > 99% (as measured by Elemental Analysis) | 1 |
PbCl2 | 99.999% | 1 |
PbI2 | 99.999% | 4 |
DMF | 99.8% | n/a |
Now selling bulk orders of 30ml with a 25% discount over our standard order sizes.

Usage Details
Fabrication Routine for Perovskite Precursor Ink I201
Glass / ITO / PEDOT:PSS / CH3NH3PbI3-xClx / PC70BM / Ca / Al
For complete step-by-step instructions please see our Full Perovskite Solar Cells Fabrication Video or written fabrication guide. Please note, however, that the routine in these full guides differs slightly to the optimised routine for the I201, which is designed to be processed in a nitrogen filled glove box.
The summary below outlines the key steps required when processing I201 ink. You can also download this summary as a PDF in order to print and laminate it for us in a clean room.
1. Substrate clean (in air):
- Sonicate ITO substrates for 5 minutes in hot (70°C) 1% Hellmanex
- Dump-rinse substrates twice in boiling, deionised (DI) water
- Sonicate for 5 mins in IPA. Dump-rinse twice in boiling DI water
- Dry the substrates with nitrogen gun
- Bake the substrates on a hotplate at 120°C.
2. PEDOT:PSS anode preparation (in air):
- Filter AI 4083 PEDOT:PSS using a 0.45 µm PES filter
- Dispense 35 µl of the filtered PEDOT:PSS solution onto the heated ITO substrate spinning at 6000 rpm for 30s
- Place substrate onto a hotplate at 120°C
- After all ITO substrates have been coated with a PEDOT:PSS layer, transfer all to a nitrogen-filled glove box and place onto a hotplate at 120°C for 20-30 mins
- Remove the substrates from the hotplate and allow to cool at room temperature.
3. Perovskite deposition (in nitrogen glove box):
- Heat I201 ink for 2 hours at 70°C and then cool to room temperature
- Place the ITO coated substrate (at room temperature) onto the spin-coater and spin the substrate at 4000 rpm (for 30s)
- Dynamically dispense 30 µl of I201 ink
- Place substrate back onto the hotplate (in the glove box) at 80°C
- Once all substrates have been coated, anneal for 90 mins
- After 90 mins, use a cleaning swab dipped in a small amount of DMF solvent to wipe the cathode stripe clean
- After cleaning, anneal for an addition 20-30 mins at 80°C to remove any residual DMF solvent
- After this time, remove substrates from the hotplate and cool to room temperature.
4. PC70BM deposition (in nitrogen glove box):
- Prepare a solution of PC70BM at 50 mg / ml in chlorobenzene and stir for 3 to 5 hours
- Place perovskite coated substrate onto the spin-coater and spin at 1000 rpm
- Dispense 20 µl of PC70BM solution onto the substrate (while spinning) and spin for a total time of 30s.
5. Cathode deposition:
- Thermally evaporate a calcium/aluminium cathode (5 and 100 nm respectively) through shadow-mask
- Encapsulate devices using a glass coverslip and encapsulation epoxy
- Expose to UV radiation (350 nm) for 30 mins to cure epoxy.
Perovskite Photovoltaic Device Performance
Below are device characteristics for our best pixel fabricated using the I201 fabrication recipe described above.
JV curves demonstrate the hysteresis observed from the device and include device metrics for both forward and reverse sweeps. The pixel presented (from a reverse sweep) had a power conversion efficiency of 11.8%, a Voc of 0.91 V, a FF of 79% and a Jsc of -16.5 mA/cm2.

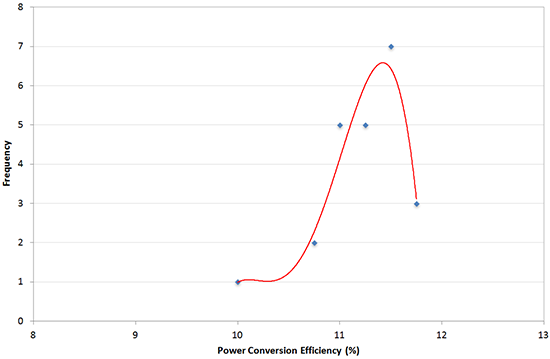
To the best of our knowledge the technical information provided here is accurate. However, Ossila assume no liability for the accuracy of this information. The values provided here are typical at the time of manufacture and may vary over time and from batch to batch.